Top 5 Rapid Prototyping Software
Rapid prototyping, also known as solid freeform fabrication, is the automatic construction of physical objects with 3D printers, stereolithography machines or selective laser sintering systems. Rapid prototyping is a type of computer-aided manufacturing (CAM) and is one of the components of rapid manufacturing. The first techniques for rapid prototyping became available in the 1980s; traditionally they have been to produce models (prototypes). Nowadays, they are increasingly employed to produce tools or even to manufacture production quality parts in small numbers. Many sculptors use rapid prototyping models in fine art exhibtion.
Read More: Top 9 Rapid Application Development Software
In brief, Rapid Prototyping takes virtual designs (from computer aided design or from animation modeling software) processes them by transforming them into cross sections, still virtual, and then forms or manufactures each cross section in physical space, one after the next until the model is finished. It is a wysiwig process (what you see is what you get) where the virtual model and the physical model correspond almost identically. The process is similar to the construction of a topographical model where the layers correspond to the elevations in the model.
There are two main methods of rapid prototyping, which are derived from similar approaches in sculpture. In additive prototyping, the machine reads in data from a CAD drawing, and lays down successive micrometer or millimeter-thick layers of liquid plastic, powdered plastic or some other engineering material, and in this way builds up the model from a long series of cross sections. These layers which correspond to the virtual cross section from the cad model are glued together or fused (often using a laser) automatically to create the final shape. This is similar to the ancient technique of coil building a ceramic pot. The primary advantage to additive construction is its ability to create almost any geometry (excluding trapped negative volumes). One drawback is that these machines make smallish parts, typically smaller than an engine block. Monumental parts can be made by automatically carving foam with a hot wire one layer at a time. Several companies have built large scale machines to do this automatically, but most market the product rather than the machine.
The subtractive method is older and less efficient. In this technique the machine starts out with a block of plastic or wax and uses a delicate cutting tool to carve away material, layer by layer to match the digital object. This is similar to a computer numerical control (CNC) device such as a lathe or a mill. The subtractive method (and CNC) is older and tried and true. It is similar in concept to a sculptor carving a block of marble or wood where they chip away at the surface of the model until the form of the project begins to emerge. Complex shapes and forms with undercuts are more difficult to accomplish with the subtractive method. Typically these are made in parts and fit together. Subtractive technologies are capable of doing large scale projects.
The standard interface between CAD software and rapid prototyping machines is the STL file format.
Today its possible to make very high solutions in layers of mikrometer and below, uv curing materials are based on Sol-Gel materials, acrylates, epoxies and others.
The word “rapid” is relative: construction of a model with contemporary machines typically takes 3–72 hours, depending on machine type and model size. Used in micro technologies “rapid” is correct, the products made are ready very fast and the machines can build the parts parallel.
Advances in technology allow the machine to use multiple materials in the construction of objects. This is important because it can use one material with a high melting point for the finished product, and another material with a low melting point as filler, to separate individual moving parts within the model. After the model is completed, it is heated to the point where the undesired material melts away, and what is left is a functional plastic machine. Although traditional injection molding is still cheaper for manufacturing plastic products, soon rapid prototyping may be used to produce finished goods in a single step.
Other advances may include machines that are both additive and subtractive. Some consider the lamination technologies (laminated object manufacture) to already be dual strategy machines.
Lab tests have shown that prototyping machines can also use conductive metals as a building material, and conceivably in the future could assemble small electronics like mobile phones in a single process.
Due to the high degree of flexibility and adaptability required by many rapid prototyping techniques, these applications typically require the use of robots or similar mechanisms.
However, there are currently several schemes to improve rapid prototyper technology to the stage where a prototyper can manufacture its own component parts. The idea behind this is that a new machine could be assembled relatively cheaply from raw materials by the owner of an existing one. Such crude ’self-replication’ techniques could considerably reduce the cost of prototyping machines in the future, and hence any objects they are capable of manufacturing.
Top 5 Rapid Prototyping Software:
BALSAMIQ
Balsamiq is a rapid wireframing tool that helps you Work Faster & Smarter. It reproduces the experience of sketching on a whiteboard, but using a computer.
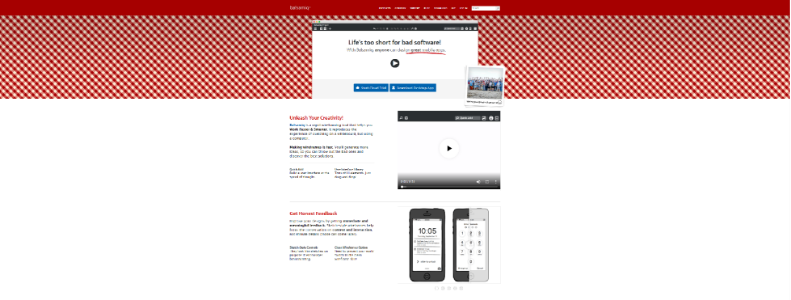
BALSAMIQ
SPACECLAIM
SpaceClaim, the leading provider of 3D Modeling software, develops the fastest way to create, edit, and repair 3D models.
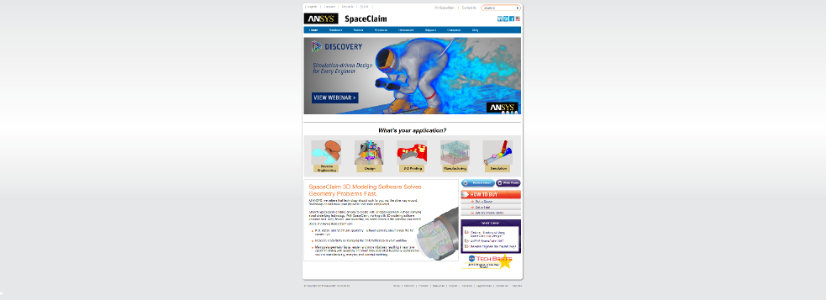
SPACECLAIM
ETAS
ETAS provides innovative solutions, engineering services, consulting, training, and support for the development of embedded systems for the automotive industry and other sectors of the embedded industry.
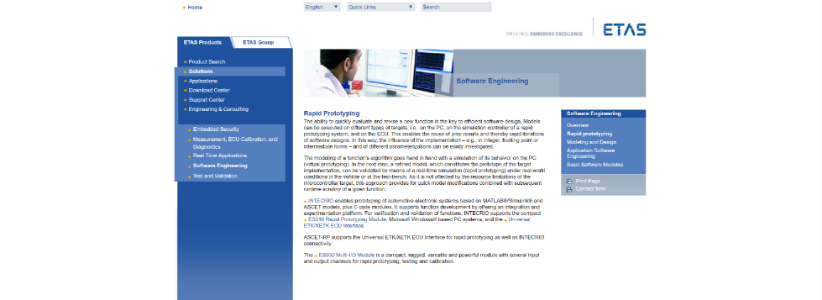
ETAS
INVISIONAPP
InVision is the digital product design platform used to make the world’s best customer experiences.
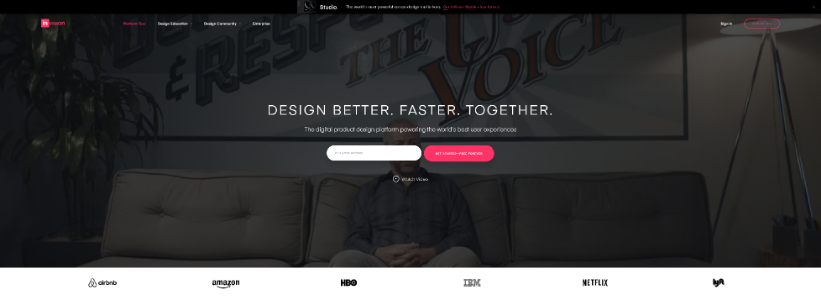
INVISIONAPP
DENTALWINGS
DWOS Rapid Prototyping CAM Software The link between the DWOS CAD applications and the manufacturing of crowns and other dental prosthetic elements with 3D printing equipment. Integration with 3D printers With its optimization and automation features, DWOS Rapid Prototyping provides a fast path to 3D-printed partial frameworks, full contour crowns and dental models.
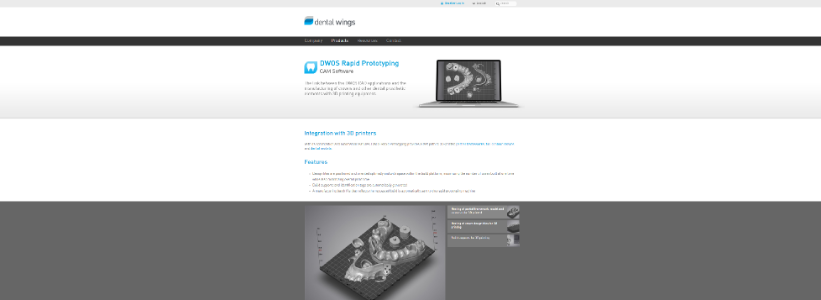
DENTALWINGS
Personal contact info – slikgepotenuz@gmail.com
Permanent Address :- Montville, NJ
CEO and co-founder at Cloudsmallbusinessservice.com