Top 11 Best Enterprise Quality Management System Software
Automated quality management software systems can provide valuable tools for administrators and managers and are indispensible tools for ISO-compliant companies. These advanced software systems typically incorporate a variety of elements designed to promote the principles, goals and standards outlined in the company’s quality management system and provide cohesion and connectivity between the various departments and functions of the company.
While each company’s workflow structure and quality management needs are different, these integrated software systems typically feature a number of common elements that roughly correspond to the eight principles outlined in ISO 9000:2000 and ISO 9000:2008. These software elements usually include training modules, document control, nonconformance handling, customer service components, corrective and preventative actions and overall auditing and trend analysis for ongoing and one-time incidents.
Training
Automated training courses are an ideal way to introduce employees to new tasks and new workflow procedures. These customized software packages can provide online examinations for employees and can manage one-on-one webinar and seminar training sessions as well as large scale classes for new employees. From initial employee orientation to the complexities of the most difficult and critical tasks, quality management software can make training more consistent and more relevant for staff members. This can lead to improved performance on the job and a reduced learning curve for new activities. Companies can track training activities more effectively as well, helping them to identify areas where additional training may be beneficial to business operations.
Document control
Tracking and maintaining copies of electronic and print documents in a centralized location is an important tenet of quality management. Quality management software offers a convenient and integrated way to manage routing, tracking, review, approval and dispositions of various documents and to provide a comprehensive record of these materials for later review. Additionally, some software programs allow searching of these documents in order to more quickly retrieve necessary information and to provide a historic record of the company’s activities.
This provides additional avenues for auditing and analysis of company operations from both a current and a historic perspective. Forms-based systems offer the highest degree of automation, but may limit the information available within the system to an unacceptable degree depending on the needs of the particular company.
Nonconformance handling
The heart of any quality control system is in its identification and treatment of problems and nonconforming materials within the existing system. Nonconformance handling software typically identifies areas of concern and personnel who should be involved in addressing the situation, with avenues for one-time solutions as well as workflow changes and process adjustments to prevent these nonconformance events in the future. Nonconformance handling software typically tracks and records these events as well to ensure the best possible record is available for later review by management.
Managing customer service issues
Customer complaints are not only a problem for businesses, but also present opportunities for growth and change. Quality management software can help monitor and classify customer complaints while providing automated avenues for resolving these problems faster and more efficiently. This can boost the company’s overall reputation for customer service while maintaining data on how these situations were resolved with the consumer. Additionally, maintaining a clear record of customer complaints can provide valuable information to auditors and quality control managers throughout the company and help to avoid further problems in the future.
Corrective and preventative actions
Tracking incidents that require corrective and preventative actions by the management team is crucial to any quality management system. Software modules that monitor, track and guide the response to these events are essential elements in the overall quality control process and can provide valuable information on appropriate measures to prevent similar occurrences in the future. By standardizing the response to these events through automated guidance systems, companies can often ensure that they behave consistently in similar situations, avoiding any sticky legal issues that might arise from responses to those situations. Additionally, the tracking capability built in to the software allows company managers to identify trends and problem areas in order to construct more comprehensive solutions to the issues involved.
Read More: Top 10 ISO 9001 Document Management Software
Auditing and trend analysis
The degree of recordkeeping available throughout the quality management software system typically allows for more comprehensive audits and evaluations of the system, making it much easier for managers and quality control personnel to identify trends and analyze available data more rapidly. Because all data is stored in a centralized location, it can often be integrated into new or existing cloud computing systems and made accessible to quality control managers in branch offices as well, providing a more comprehensive analysis of the overall performance throughout the company.
Most quality management software solutions support a variety of electronic records and can store and transmit these records for analysis and future use. Additionally, some systems include calibration and quality control information for manufacturing, making them ideal for the factory environment. Regardless, the principles of quality management can be made more accessible and easier to achieve by incorporating advanced quality management software into the workflows and processes already in place within most corporate environments.
Top 11 Best Enterprise Quality Management System Software:
VERSESOLUTIONS
Verse Solutions provides Total Quality Management (TQM) Software that enables manufacturers of all sizes to mitigate compliance management. Features/modules include: Document Control, Employee Training, Corrective Action, Audit Management, Risk Register and Centralizes Reporting.
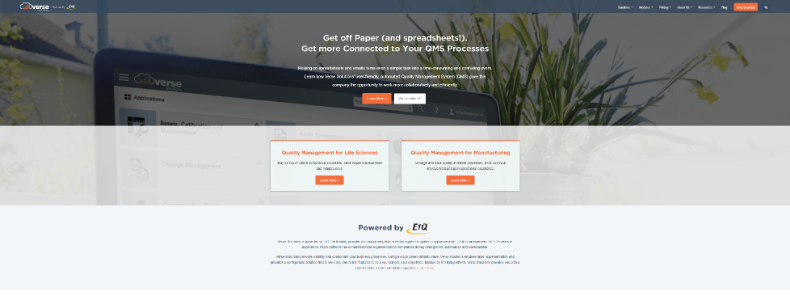
VERSESOLUTIONS
ASSURX
Quality Management System (QMS) Software + Compliance Management Software for regulated businesses. One versatile system simplifies + improves operations.
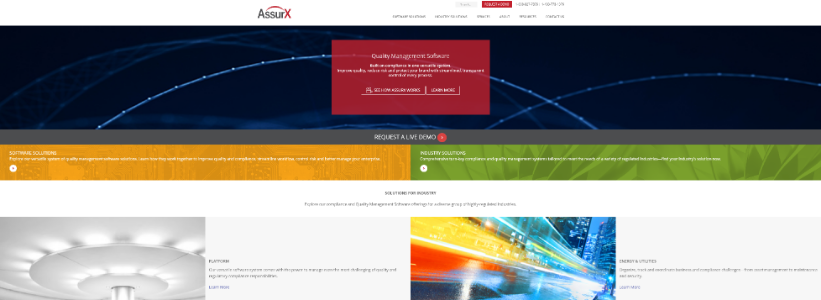
ASSURX
INTELEX
Intelex cloud-based software manages environment, health & safety, quality and suppliers for regulatory compliance, and streamline ISO initiatives.

INTELEX
DONESAFE
Donesafe will help you comply with regulations, protect people and assets, streamline business processes and foster a culture of environmental, health and safety & quality (EHSQ) excellence.
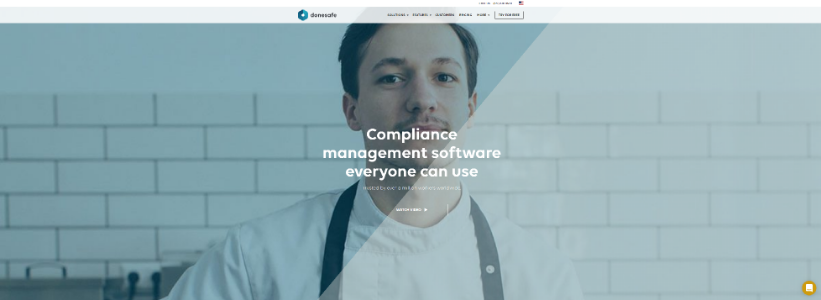
DONESAFE
CAQ
The definitive CAQ-System. CAQ covers every aspect of computer aided quality assurance and was designed with the highest degrees of adaptability and customizability in mind.
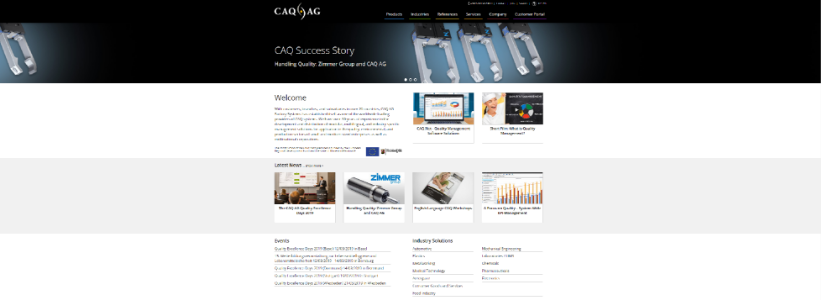
CAQ
ETQ
ETQ offers the leading Quality Management Software, EHS Software & Compliance Management Software for improving quality & preventing high-risk events in organizations.
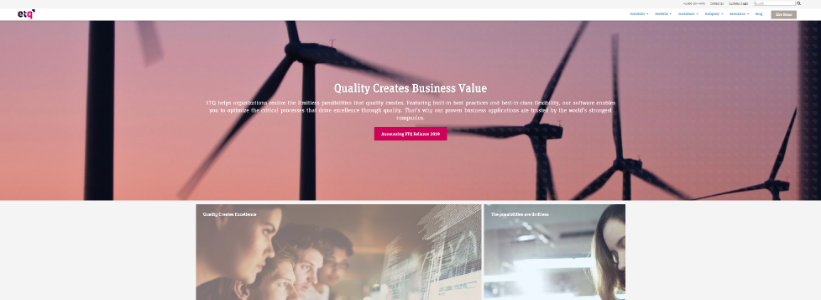
ETQ
METRICSTREAM
MetricStream provides Governance, Risk and Compliance (GRC) software solutions that allow companies across various industries to streamline and automate their enterprise-wide GRC programs.
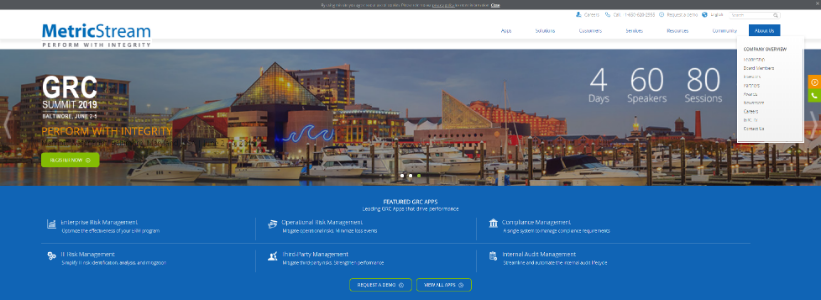
METRICSTREAM
SPARTASYSTEMS
Sparta provides TrackWise quality management system (QMS) and regulatory compliance software. Replace your paper-based QMS systems with centralized and fully integrated quality management software. Learn more about TrackWise quality software.
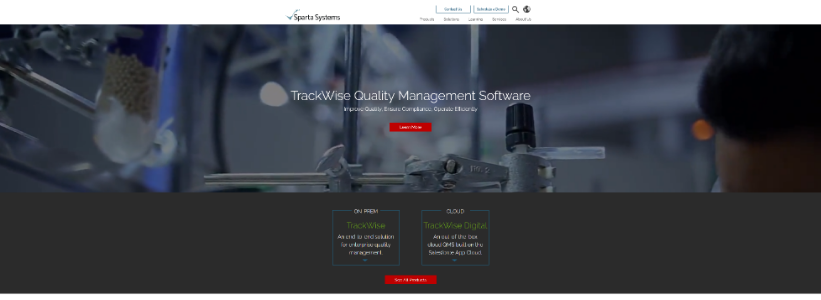
SPARTASYSTEMS
MASTERCONTROL
Document Control Software, Document Management Software Systems: quality and document management software for electronic document control, workflow, collaboration, electronic SOP, corrective actions, preventive actions CAPA, nonconformance for ISO 9000, ISO 14000, QS-9000 and FDA 21 CFR Part 11, GxP-compliant companies.
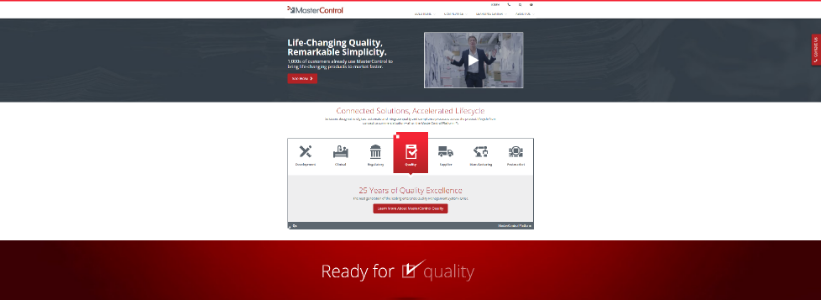
MASTERCONTROL
ISOLOCITY
Automated quality management software with part inspection, CAR, document management, internal auditing, real time spc, HR & more. Get your free trial.
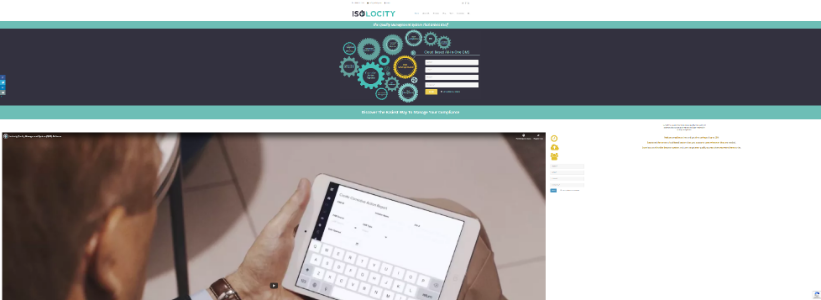
ISOLOCITY
CORITY
Quality Management Software Cority’s true SaaS solution for Quality management Request a demo Leave the paper behind. Companies understand the importance of Quality. Controlling nonconformances and quality issues before they are released into the supply chain is how companies reduce costs, protect customers and maintain their brand reputation.
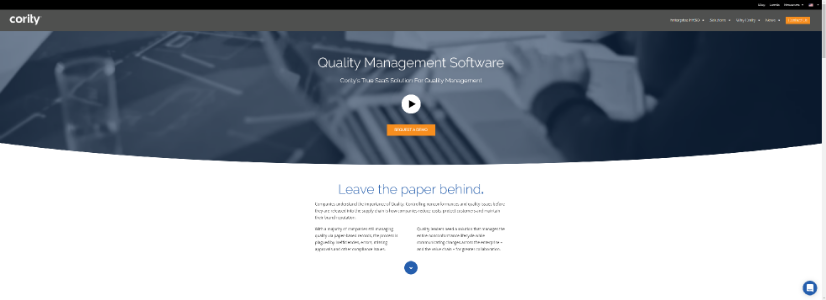
CORITY
***
Introduction
The mass production of goods changed the concept of “quality.” Before the advent of mass production, a product or good would be created by one tradesman or craftsman. During this process, the craftsman would monitor or “manage” the quality of the good from the start of the process to its finish. Each craftsman’s quality management system was designed specifically for whatever industry or trade in which he was involved. A potter would have different steps in his quality management system than a blacksmith, but both the potter and the blacksmith would have a system of inspecting each product they made to make sure it adhered to their standards of quality.
Mass production divided the different stages of the manufacturing process in such a way that no one individual could supervise all stages. The best way to visualize the effects of mass production on quality management is to compare the manufacturing process of a piece of pottery to that of an automobile. A modern automobile has hundreds of different individual processes, from the assembly of the engine to the production of the door handle. Monitoring the overall quality of the automobile requires inspecting each individual part and process to make sure it meets required standards. Because of the complexity of each sub-process, no one inspector has the considerable expertise necessary to effectively manage the overall quality of an automobile. Dozens of separately qualified inspectors are needed. The quality of a piece of pottery, on the other hand, can be inspected by one individual. In order to maintain consistent standards of quality in a mass production environment, a new system of quality management was required.
A brief history
William Edwards Deming was a Yale educated statistician who taught engineers how to substantially increase production of supplies during World War II. He later expanded his theories to include notions of quality control. Japanese engineers and scientists invited him to expound on these principles in the 1950s. During the same time period, the Japanese also invited electrical engineer Joseph M. Juran to teach them his theories on quality management. Juran had developed his theories while working for Western Electric. These two men, along with William A. Shewhart, are credited with developing the contemporary system of quality management.
The Japanese companies that applied these principles of quality management experienced increased productivity and much higher profits. In the following decades, Japanese products eventually became competitive with long-established manufacturers because the “quality” of their products had increased. This real-world case study of the effectiveness of the quality management system encouraged manufacturers around the globe to adopt similar practices.
The Principal Components
As explained above, the specific steps of each quality management system (QMS) are designed for a particular industry. The QMS of an automobile maker will be different than the QMS for a lightning manufacturer. Regardless, each QMS has several basic components. These components include knowledge management, a clear organizational structure, a definition of product quality, an emphasis on customer satisfaction and a provision for regular maintenance of the process in an attempt to keep it sustainable. We will now review each component in greater detail.
1. Data/Knowledge Management
Knowledge or data management is a process whereby a company or organization keeps track of its information. This information can be of a proprietary or public nature. The information can be exchanged between employees and administrators, employees and the public, or between the company and outside vendors. The information itself can be contained in a physical form such as a manila folder or in an electronic format such as a company-wide social networking site.
The way in which the information is managed has a great deal to do with who is participating in the information exchange. In a QMS, information is generally controlled by the management or administration of a particular company. The management determines what types of information can be discussed in the workplace. The management also determines how questions or comments should be handled according to the data management structure.
As an example, an employee who is uncertain how to perform a particular function may be instructed to consult a training manual. An administrator who is uncertain how to handle a disciplinary or budget problem may be encouraged to call a meeting with senior management. The “knowledge” in this case is specific to the individual involved. However, an effective QMS will anticipate all types of data management situations and outline how each case should be handled.
2. Organizational Structure/Effective Leadership
A QMS functions only if each department in the organization understands how it fits within the larger hierarchy. From the clerk in the mailroom to the CEO, each member of the organization must understand his duties as those duties relate to the overall functionality of his department. Once he understands his duties to his department, he will then understand his duties to the organization as a whole.
A QMS that is very clear about how the purpose of each department will automatically produce the right conditions for a strong leadership structure. The CEO of the company has authority over each department head. Each department head has authority over each project manager. Each project manager has authority over his team members, and so on. However, simply designing a clear-cut structure does not automatically endow the organization with effective leadership. The individuals who are nominated to be leaders within each part of the overall organizational structure must be prepared to demonstrate their ability and provide guidance for their employees. A weak individual who has been nominated to be a leader will not be effective in his role no matter how strong the corresponding organizational structure.
Therefore, in addition to designing an effective organizational structure, a QMS must also have policies for selecting effective leaders. These policies will often be based on performance factors and inherent “character traits.” These character traits may be anything from an ability to show up to work each day on time to technical skills such as an exceptional mathematical ability. Leaders may also need to demonstrate the ability to inspire productivity among their employees. Ultimately, each leadership role within the larger organizational structure will need to be defined in terms of what character traits it requires in order to keep the organization productive and effective.
3. Product Quality
The definition of “quality” in a QMS refers to the functionality, usability and consistency of a product. A chair that breaks when someone sits in it does not meet the quality standards for a chair, in the same way that a car that doesn’t start or a refrigerator that does not keep food cool also fail to meet quality standards.
Each QMS is structured to produce products that meet these basic notions of quality. Usually, the production of the product is broken down into discrete processes. Each process is then analyzed so that it is not only efficient but will meet the quality criteria for that particular product. This is both cost-effective and guarantees that thousands of units of a given product can be produced without requiring the personal inspection of a manager.
4. Customer Satisfaction
Mass production works as a economic model because a consumer class can be counted on to buy the products. However, this consumer class will only buy the product if it satisfies their needs. Frequently, the material quality of the product is only part of what goes into “customer satisfaction. Customers need to feel that they can rely on the company that manufactured the product in case of an emergency or product malfunction. If a customer has a complaint, the customer needs to have an appropriate forum where she can address her concerns.
In order to be effective, a QMS must also design a process for dealing with customers. This process must make the customer feel appreciated while using the minimum amount of company resources. Many QMS set aside a separate “customer service” department to handle customer complaints or queries. This department employs procedures that allow the customer to vent their frustrations in as timely a manner as possible. The goal of the customer service department is to ensure that after the customer has gone through the customer service process, she will have a positive impression of the company and its products.
5. Maintenance/Sustainability
Each QMS is designed to foster the highest quality, productivity and efficiency at the lowest cost. However, no QMS can remain effective without constant modifications. The mark of a truly great QMS is that those who formulate it understand the importance of continued improvement.
The economy, employee benefits and availability and pricing of supplies are factors that no one organization can control. A QMS is designed to produce products with the understanding that these factors will remain relatively stable. As an example, an automotive company that uses a substantial amount of raw zinc in its manufacturing process will undoubtedly have a QMS that designs procedures around a base price for the zinc. The QMS may allow for price fluctuations of 1 to 5 percent in the base price of zinc. However, if the price of zinc should suddenly increase by a factor of 1,000 percent, the QMS will need to be redesigned to reflect this change.
This need to redesign can also be triggered by sudden shifts in the economy or in labor practices. Imagine a company that pays 15 percent of its net revenue for employee expenses such as worker’s compensation insurance and payroll. If labor practices shift and require the company to pay 20 or even 30 percent of its net revenue for employee expenses, the old QMS will no longer be effective.
However, a QMS must also be designed in order to remain sustainable. A company that has been in business for over 100 years has a QMS that can be modified to adjust to temporary fluctuations in the market, but that also encapsulates the underlying principles of that particular industry. A company that mass produces carpet, for example, should be able to remain in business for as long as people want carpet in their homes. The QMS may have to be altered to reflect different material prices or labor practices, but its basic infrastructure should be designed to reliably produce quality carpet at a price that guarantees profit for the company.
International Standards
The International Organization for Standardization has created a certification process for the development of services and products. This standard, known as ISO 9001:2008, has a provision which specifically addresses the need for continued improvement of an organization’s QMS. Several other countries have similar organizations or awards that are dedicated to maintaining a high level of quality in an organization in terms of its products and management procedures.
Future of Quality Management Systems
No one knows precisely what the impact of the information age will be on the formulation of quality management systems. The future of quality management systems will likely be shaped more by changes in consumer spending habits and production methods. If the economy returns to a model where products are produced individually and sold to a small group of consumers, the current complexity and scope of quality management systems will be unnecessary. On the other hand, if typical production processes continue to use a mass production model, the need for ever more complex and nuanced quality management systems will continue.
Understanding ISO Standards
ISO standards are agreed upon ways to do things. Put in place by an international body, they allow organizations, government and companies all over the world to follow set procedures. This makes it easier for groups to talk to each other and for products to work together.
The International Organization for Standardization is based in Geneva, Switzerland and is made up of each country’s national standardization institute. Currently, institutes from 163 countries, including the USA’s American National Standards Institute (ANSI) and Germany’s Deutsches Institut für Normung (DIN), are members of the ISO. Founded in 1947, it has published over 19,000 standards spanning a wide range of endeavors.
Many ISO standards define how devices work or should be made. For instance, the reason that standard Ethernet cables with RJ-45 connectors are interchangeable with other Ethernet cables all over the world is that Ethernet follows an ISO standard, numbered 8802-3. Digital cameras all have the same light sensitivity, with the 100 setting much less sensitive than the 400 setting, because camera light sensitivity levels are also set by an ISO standard – ISO 12232:2006. European A4 size paper is always the same size because its dimensions are defined by the ISO 216 standard. Finally, ISO 20126 specifies how toothbrushes should be designed and tested to, among other things, ensure that their bristles do not fall out.
Other standards define broader practices. Companies looking to ensure that their manufacturing processes lead to products of consistently high quality will follow the ISO 9000 family of standards. The ISO 14000 family specifies techniques for environmental management to help organizations put processes in place to minimize the damage that they do to the ecosystem. Without creating formal standards, the ISO also gives guidance on topics such as social responsibility and risk management through their 26000 and 31000 standards, respectively.
To understand the benefit of ISO standards, consider the impact of ISO 216. The widespread acceptance of ISO 216 means that A4 paper from any manufacturer can be used in any printer designed to use A4 paper. It also means that a design made in a piece of software that supports the A4 paper size will print in the same position on the page on any piece of A4 paper. Without a standard, pieces of paper would be different sizes, potentially not fitting in printers. Each program could interpret A4 differently, leading to printouts that do not fit on the page or that come out off-center. By having a third-party let the world know that a piece of A4 paper is 210 mm wide and 297 mm long, everyone can design to that specification.
ISO standards also work with management processes. For instance, the ISO 9001 quality management standard spells out how a company can set itself up to ensure that it follows other standards to make products of high quality. Companies can look for ISO 9001 certification to know that their vendors have not only committed to quality production but also that they have done it in a manner that has been successful for companies all over the world.
The ISO constantly develops new standards. Typically, demand for standards comes from organizations who request development of a standard from their company’s standardization organization. The national organization then lodges a request with the ISO committee responsible for that area of standardization. If the ISO decides to move forward, a standard is developed by global experts and vetted with public input. The ISO typically only issues standards with global impact. While beach safety flags, for instance, are defined by ISO standard 20712, the ISO would not issue a standard on how to make a Canadian or Gabonese flag, since those are of national importance.
ISO standards make the world work better. By having a single global organization, products and processes can be synchronized. Even more than the benefit of synchronization, ISO standards also share best practices. Typically, ISO standards represent the world’s best thinking on how to accomplish a given task. This quality is what makes the ISO standard such a major contributor to the high quality of the services, products and procedures in the modern world economy.
Developing a Quality Management Plan
Businesses simply cannot be successful without implementing a quality management plan. Quality management is vital in every type of company and is the cornerstone to a business providing lasting, consistent service. While quality management planning is essential, many businesses do not know exactly how to begin the development process. It is important to understand the basics of developing quality management, whether the plan is meant for a specific department, a project within that department, or for the company as a whole.
Prior to the development of a quality management plan, it must first be determined what the exact purpose of the plan is. Quality management offers a basic structure upon how quality is assured during a project or throughout the course of business. In almost all cases, the plan also serves as an accountability measure by providing feedback and documentation to management. The best plans are also made available to customers so that they are aware of the importance placed on quality service.
For a particular plan, the person, team, or committee that is forming the guidelines must first define the quality management plan so that all of those encompassed by the plan are precisely aware of what their own expectations should be. Plans must be well written, easy to understand, and readily accessible.
Step 1: Defining Quality Policy
Perhaps one of the most difficult aspect to developing a quality management plan is defining exactly what the quality policy is. Often, a quality assurance team is made up of a variety of individuals, each with their own ideas about what quality means. It is important to try not to encapsulate too many thoughts into one policy. Instead, attempt to focus on the core values. A simple, yet effective, way to start is by looking over the quality policies of well respected organizations. Find those in any given field that seem to have a firm grasp on the quality practices your organization wish to emulate. It is not necessary, or even wise, to copy another company’s quality policy statement, but it can offer an excellent basis for developing your own.
Step 2: Determine the Quality Approach
Once the quality policy has been decided upon, the practices required for reaching the quality levels needed must be determined as well. Sometimes referred to as the “process approach,” these guidelines should detail explicit instructions on how quality levels are obtained. The approach generally includes methods for extensive reviews, at the committee, management, and even customer level and how these reviews will be utilized to assure quality practices.
Step 3: Compile Reference Materials and Documentation
A quality management plan cannot exist without the appropriate support documents. Individuals who are affected by the quality management plan should have access to any documentation that concerns them directly. This includes an explanation of the quality policy and the quality approach as well as any forms, flowcharts, or reference materials that may help the project and/or company to succeed. There may also be a system put into place that allows for updates of materials as the quality management plan is implemented. Employees, management, and even customers may be interested to learn about the increase in accountability and the high level of quality achieved through successful implementation of the plan.
In some cases, the material included with quality management plans will also contain certain quality standard documents. This is true of companies that are following the ISO 9000 family of standards or similar management systems.
Personal contact info – slikgepotenuz@gmail.com
Permanent Address :- Montville, NJ
CEO and co-founder at Cloudsmallbusinessservice.com